Hi Turkotekers,
Since I am affected by a
strong case of «l’esprit de l’escalier», I realize only now that I have
not answered convincingly enough Dinie’s and Steve’s
concern:
Quote:
«
I have read that it (indigo) does not really
penetrate the fiber, but forms a kind of coating on the outside. That was
why jeans fade so well and why a green made by dyeing blue over yellow,
tends to become yellowish. Indigo rubs off. Is this
correct?»Dinie’s remark in a previous post is partly correct:
Even seasoned denim dyer’s do indeed believe and write,
erroneously, that indigo stays all on the surface of the cotton
fibre, forming layers of pigment and that it is the cause of the peculiar
fading of jeans. By analogy many ruggies believe that indigo sits on their
favorite rug surface too.
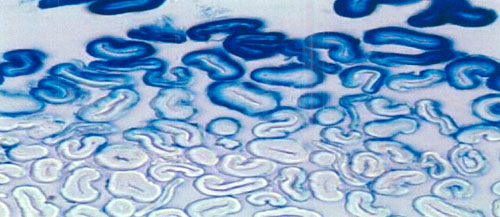
In fact, as this
micro-photography of a cross section of a denim warp clearly shows, even
in a dyeing process specifically designed (*) to keep reduced indigo
(«leuco») from penetrating too deeply into cotton, the external individual
cotton warp fibrils are indeed penetrated by the dye, which forms a
so-called «ring dyeing». The very short contact time and low dyeing
temperature explain that the dye-bath only wets properly the external
fibrils of the warp, but even under these, purposely unfavorable, dyeing
conditions the leuco molecule quite easily penetrates any single cotton
fibril which it is allowed to meet.
The picture also shows a few
agglomerates of «surface dye» (for example on top of the first fibril on
the left). Given the low affinity of leuco for cotton, its strong tendency
for premature oxidation (back to indigo pigment) and the peculiar dyeing
process, a significant amount of indigo on the surface is unavoidable.
However most of it is eliminated from the warp yarn at the end of the
dyeing process, during a two-steps (hot & cold) wash-off
operation.
The famous «stone-washing»
performed on the jeans garment
is something different: It is a severe treatment of the textile
surface with pumices, which rubs-off some of the surface
fibers and
the ring dyeing of others fibers, showing the white parts.
A mere
elimination of indigo agglomerated on the fibre surface would not call for
such a hard abrasion.
In dyeing of rug wool with indigo, the
pre-industrial dyer did his very best to avoid deposits of pigment on the
yarn surface (thoroughly pre-wetting the wool to get air out of the fiber,
keeping it under the dye-bath surface to avoid contact with the foam of
indigo pigment which usually floats on top, agitating only very gently the
fiber, to avoid carrying air into the dye-bath, keeping the pH and the
reductive power of the dye-bath high etc.). In old recipes, one often
notes that deposits of surface dye eliminated during the final
washing-off, leave colorless spots on the fiber. No doubt one of the
causes of the typical abrash of indigo-dyed wool.
Besides, wool dyeing
conditions are much more favorable to leuco penetration into the fiber
than it is the case in cotton denim warp dyeing. Although each indigo wool
dyer seems to have his own recipe, the dyeing temperature averages 50°C
(instead of 25°C) and the dyeing time averages 30 minutes for each dip
(instead of 30 seconds).
(*)
the cotton warp yarn is dipped for
less than 30 seconds in a leuco dye-bath, at room temperature, «aired»
(exposed to air) for 60-80 seconds and this process is repeated, on
average, 6 times)Hoping that you have all recovered from
season excesses,
best regards
Pierre